The Present State
Textiles profile: Tradition, modernity and competitiveness
GKM Towfique Hassan
Textiles industry initiated the industrial revolution in England. It stimulated the initial development processes of countries like Japan, Korea, Taiwan and Hong Kong. Textile sector has traditionally played an important role in the economy of this part of the subcontinent since the Mughal days through the British era to the Bangladesh days. If our hallmark in quality handloom production was represented by muslin, jamdani and silk fabrics, the efficiency with which we have subsequently woven and knitted the garments success story owes its origin to the skill that is perhaps ingrained.
Let me begin by underscoring the contribution that the textiles sector has been making to the national economy:
- Textile sector contributes 38% of the industrial value addition and earns 75% of the total export earnings of the country.
- Around 4.5 million workforce is engaged in the textile sector of which 50% are poor women.
- The country entered the export market of RMG and Knit Products in 1978. In 1981 total export earnings from RMG were USD 3.5 million, which by the end of 2004-05 (July-June) stood at USD 6.4 billion.
- In the 1990s value addition in the RMG sector was 20% but at present the value addition is around 45%.
- 85% to 90% of the demands of Raw materials for knit garments are supplied by the local knitting and knit-dyeing mills.
- Around 25% of the total demand of woven fabrics for export of RMG is supplied by the local weaving and processing mills.
Taking into consideration the past heritage, contribution in export trade and generation of employment opportunities and also the concept of export-led growth, the government declared the textile sector as Thrust Sector in 1992.
From the viewpoint of processing, textile mills of the country could be classified as
Spinning Mills: Production of yarn from raw cotton.
Weaving Mills: Weaving of fabrics (Gray fabrics)
Dyeing-Finishing Mills of woven fabrics
Knitting Mills
Knit-Dyeing-Finishing Mills
Woven Composite Mills (A number of processes are carried on)
Knit composite Mills (A number of processes are carried on)
Hosiery units
Manufacturing of Readymade garments.
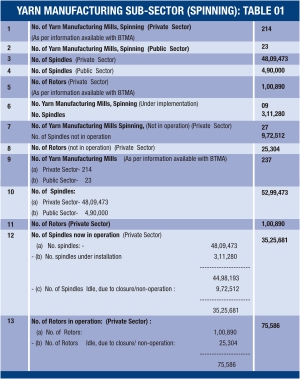
In addition to the above there are different types of textile mills where specialised processing of yarn and fabrics are undertaken such as Yarn dyeing, Terry towel, Woolen fabric manufacturing, processing and production of silk yarn and fabrics.
Nature of the structure of domestic yarn and fabric mills : Types of mills set up over the years (shown in table 01)
Spinning Mills
In the private sector there are 214 spinning mills. All these mills produce yarn and only a few are composite mills. In addition to these there are 24 mills in the Public Sector out of which 23 mills produce yarn and 1 mill produces woolen yarn and fabric .
Weaving mills (Power looms and specialised textiles):
Production of fabric from yarn goes to weaving sector. At the moment there are 356 medium to large size weaving mills, which are members of BTMA. Most of these mills produce grey fabrics and only a few produce grey and do the dyeing-finishing process to produce finished fabrics. The total production capacity of these mills is around 800 million meters. On the other hand there are around 1065 small and specialized power loom units some of which are members of the Bangladesh Specialised Textiles Mills and Power loom Industries Association (BSTMPIA), and some are not. In these units there are about 23000 power loom (shuttleless), whose yearly production capacity is around 300 million meters, but they produce only around 155 million meters. Even when there exists a tremendous demand-supply gap of fabrics, the performance of power looms and Specialised Textile Units is unsatisfactory. A number of reasons can be attributed for this state of affairs of this sub-sector: The shuttleless are obsolete and out dated, their width is very small and technology used is also outdated. As such whatever fabrics are produced in these weaving mills, these are mostly of poor quality. Therefore, the products cannot be used in the production of exportable apparels. As such only around 25% of the demand of fabrics of the export oriented readymade garments units could be met from the local source.
However, to produce high quality fabrics and to increase the production of high quality woven fabrics, a number of weaving mills with high technology having shuttlesless (Airjet, Rapier, Projectiles etc.) are being set up. On the other hand small power loom units are being set up in a scattered manner. Most of these units have 10 to 40 looms and they do not have back process machinery. Therefore, even there exists a large demand in the export-oriented units, these units cannot respond to that demand. Whatever medium or poor quality grey fabric they produce, these are supplied to readymade garments units to be used for pocketing.
Dyeing-Finishing Mills:
There are about 293 Dyeing-Printing-Finishing units in the country. Of these 115 are fully mechanised and 178 semi-mechanized. Of the mechanized units only a few are capable of processing internationally acceptable quality fabrics. These units could meet around 25% fabric demand of the RMG units. Due to lack of quality fabrics, most of the Dyeing-Finishing units cannot play their due role to provide required fabrics to RMG units. It is essential to set-up Dyeing-Finishing units with latest technology in the country to meet the fabric demand of export as well as local markets. In addition to this, the existing mills need to have a BMRE program.
Knitting and Hosiery Mills:
Presently knitting and hosiery products, such as T-shirts, Polo Shirts, Under-Garments, Bra, Panty etc. are used as readymade garments. The use of knit apparels is gradually increasing. At present there are about 700 export oriented Knitting and Knitting-dyeing-finishing units in the country. These units could meet 85%-90% demand of knit fabrics of the export oriented knit RMG units. There are also around 2000 factories producing knit fabrics using traditional technology in addition to export oriented knitting units. The produce of these traditionally managed units meet the local demand of knit fabrics.
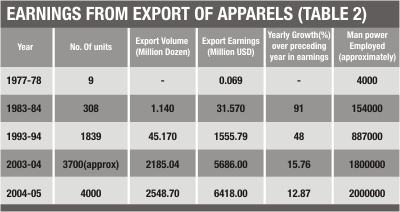
Export-Oriented Readymade Garments units (RMG):
The country entered the export market of apparels in 1978 with only 9 units and earned only USD 0.069 million. During the last two decades this sector has achieved a phenomenal growth, due to policy support of the government and dynamism of the private sector entrepreneurs. Now the number of RMG units is around 4000 and the export earnings have reached at USD 6.40 billion. The export earnings between 1977-78 and 2004-05 have been shown in Table-2.
The support policies of the government have been: Import of raw materials through back-to-back L/C, duty free import of raw materials under bonded warehouse facilities, cash incentives provided to the producers-cum-suppliers of local fabrics and accessories to export-oriented RMG units.
In table-5 we can see the total availability of fabrics, their use in local and export-oriented units between 1999-00 and 2003-04.
Figures in Million Mtrs.
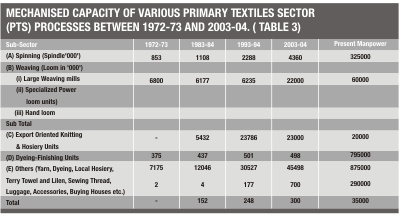
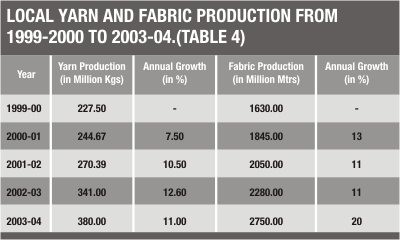
Demand-supply gap in fabrics:
The PTS is meeting the major demand of fabrics of the local markets. In addition to that a significant part of the demand of fabrics of export oriented RMG units is being met by the PTS. With gradual increase in population and expansion of trade, the demand for fabrics both in the domestic market as well as in the Export Oriented RMG Units is increasing very fast. In the year 2003-04 the demand for fabrics in the domestic and export oriented RMG units was 5188 million meters. Against such demand at present only 2750 million metres of fabrics are being domestically produced. Therefore the demand-supply gap of fabrics stood at 2438 million metres. In this regard the projection of the demand-supply gap of yarn and fabrics both at local and export market for 2008-09 has been given at table below.
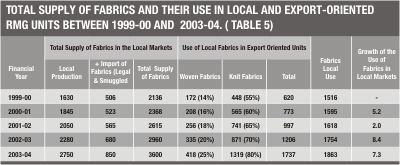
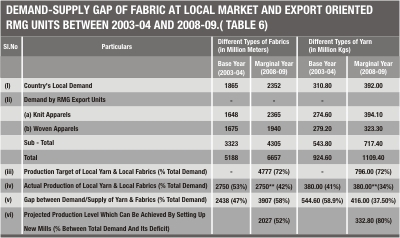
Table-6 showing demand-supply gap of fabric at local market and export oriented RMG units between 2003-04 and 2008-09.
** If no new mills are setup.
From Table-6 it is seen that in 2008-09 the demand for fabric by both domestic markets & export oriented RMG units shall be at 6657.00 million metres. Against such a projected demand, the production of fabrics was at 2750 million metres in 2003-04, which was only 42%. This indicates that there will be a shortfall of fabrics by 3907 million metres which will be 58% of the total demand. Such a staggering deficit cannot be met by a country like Bangladesh by setting up new mills in the PTS within 4 to 5 years due to fund constraints. It is not possible by any developed or developing countries to be 100% self sufficient in fabric production. Therefore, the projection of 2008-09 to produce additional fabric to the tune of 2027 million metres has been calculated into consideration establish amount of new mills (Weaving, Knitting, and Dyeing-Finishing). (As shown in table-7) On the other hand to meet the demand-supply gap of yarn by local and export oriented RMG units for fabric production will stand at 416 million kgs. 80% of this shortfall can be met by local production, if ring and spinning mills are established.
Projected number of new textile mills along with investment outlay in the Primary Textiles Sector (PTS) covering spinning, weaving, dying and printing.
A projection has been made to find out the demand-supply gap of yarn and fabrics in the year 2008-09. Along with projection an investment outlay has also be made in the major textile sub-sectors as in Table-7.
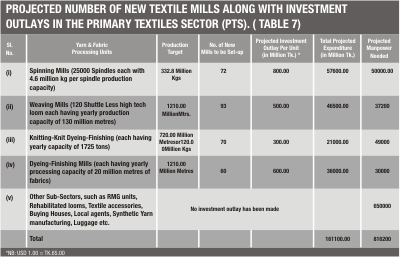
From Table-7 table it is seen that if 72 Spinning mills, 93 Weaving mills, 70 Knitting-Knit-Dyeing units and 60 Textile processing mills are established by 2008-09, the demand for yarn and fabrics could be met. However, there will be a fund requirement of Tk. 161100.00 million for setting up those mills and production units. If established, job opportunities for the 8 million workforces could be created within the next 5 years.
Nature and production capacity of newly proposed mills under various sub-sector of textile sector
Normally in the textile sector mills are set-up either with various processes in the form of composite mills or having independent single process, such as Spinning, Weaving, Knitting, Knit-Dyeing-Weaving-Dyeing-Finishing. From para 2.1 of this article it can be seen that the number of composite mills having 3-stage process is highly limited in number. The reason behind this can be attributed to huge investment outlay. Normally it involves around USD 40 to 50 million to set-up a 3 stage processing composite mill. In such a situation entrepreneurs are discouraged because of the impossibility of providing equity to such high investment outlay. Further it has been seen from national and international experience that it becomes very difficult to maintain quality of the product, maintain compatibility and ensure efficient management, when it comes to running and managing composite mills with 3 absolute separate stages of processing.
On the other hand entrepreneurs are more interested in setting up independent spinning and weaving mills in the private sector. However, in most cases setting-up of independent spinning or weaving miils along with dyeing-finishing facilities is more popular. In this regard it may be mentioned here that of late quite a number of knitting, knit-dyeing or knitting, knit dyeing and RMG units combined together have been either set-up or in the process of setting-up.
Assistance Fund for development of the sector
With the phasing out of the MFA, the global textile trade is now free from quota restriction. Now the textile trade is to be governed by GATT discipline. The phasing out of MFA has created a tough competitive environment, where Bangladesh will have to compete with countries like China, India, Pakistan, Thailand, Indonesia, Korea who are very strong in the production of fabrics. If Bangladesh is to compete with them on equal footing, we need to be self-sufficient in the production of fabrics. Therefore, an investment fund needs to be credited to extend support to local entrepreneurs.
To accelerate the pace of investment in the PTS a proposal has been noted to set-up in Textile and Garments Development Assistance Fund. We are already aware that there is a need of Tk.160000 million to set up spinning, weaving, knitting-knit-dyeing mills by 2008-09 to bridge the demand-supply gap of yarn and fabrics. The govt. realized the importance of this sector and therefore, declared this sector to be a “Thrust Sector” under the present industrial policy. However, financial support was not provided in the past to encourage investment in this sector. As such the PTS as well as RMG units failed to achieve the desired level of production capabilities. Therefore, it is felt that a fund should be created by the govt. to encourage investment in the textile sector. Through this fund various textile sub-sector be provided loan through the banking channel. Neighboring country India has long ago in the 1st part of 1990s, set up a fund known as Technology Upgradation Development Fund Definition of Textile Technology, Up-gradation, Type of Textile Machinery eligible, Size of Fund Scheme, Promoter contribution, Debt-Equity Ratio, Rate of Interest, Repayment of loan etc. have already been prepared by the Textile & Jute Ministry and submitted to Ministry of Finance and National Coordination Council (A council headed by Principal Secretary to the Hon' ble Prime Minister) for Textiles and RMG for consideration.
Problems of the Primary Textiles Sector (PTS)
There exists a misconception that there is a conflicting interest between the PTS and the Export-Oriented RMG units. Actually the success or failure of these two sectors is interrelated. PTS suffers from a number of defects that are hampering its growth and deterring it from playing the desired supportive role to RMG units. Those are enumerated below :
(i) The entrepreneurs are discouraged to invest in PTS due to very high debt - equity ratio.
(ii) The long-term interest rates on loan for new industries in Bangladesh is very high (Bangladesh 9-12%, Pakistan 5%, India 6%) compared to competing countries.
(iii) Till date no fund for assistance to textile sector has been created.
(iv Leakage from Bonded warehouses and smuggled fabrics deter the growth and development of PTS.
(v) Due to provision of subsidy and other incentive at different stages of production process by the competing countries, their PTS products are more competitive than ours in the international market.
(vi) Dearth of trained manpower of international standard.
(vii) Poor labour productivity and inconsistency in the quality of textile products, our products are uncompetitive in international market even though the labour costs are low.
(viii) Due to operation of obsolete production techniques and acute shortage of technically sound manpower, weaving and weaving-dyeing-finishing sub-sector could not make significant headway.
(ix) Production capacity of old mills are extremely low due to use of obsolete technology. This was compounded by poor quality of manufacture.
Recommendations/suggestions to solve the problems of PTS and make that highly competitive for international as well as domestic markets.
Keeping in mind the changing trading environment with the phasing out of MFA, trends in international trade, in textiles for local manpower both in PTS and Export Oriented RMG units, the following recommendations are made to make textile sector as a whole viable and sustainable.
(i) The debt-equity ratio be fixed at 70:30 or at least to a favourable range.
(ii) To reduce the demand-supply gap of fabrics and yarn an investment of Tk.160000.00 million shall have to be made in the backward linkage industries in the textile PTS in the next 5 years. Half of this may be provided by the entrepreneurs as equity or agents for foreign direct investment. Rest half may be provided by banking channel on the basis of bank-client relationship.
(iii) Necessary instruction be issued by the Bangladesh Bank to finance the following backward linkage sectors on priority basis.
a. Dyeing and finishing of woven fabric
Weaving
b. Composite knit
c. Specialised spinning (manmade fabric-based)
d. Spinning (Ring and Open-end)
Priority may be given to those units which will be employing the retrenched/terminated workers of RMG units closed down due to adverse impact of MFA phase-out.
(iv) A special fund of Tk.80,000.00 million shall be made available at an interest rate of 7%, 2% less than the present bank interest rate. The 2% difference be subsidised by Bangladesh Bank (Central Bank) under a refinancing scheme.
(v) Import of textile spares, dyes and chemicals and sizing materials be made duty free.
(vi) Rebate may be allowed to utility bills like electricity and gas etc. subject to regular and timely payments.
(vii) A cash assistance @ 15% be given for using local yarn/fabrics for export of apparels to make them competitive in the post MFA regime.
(viii) Training programme be introduced to produce efficient and experts workforce and personnel in the field of textile production, so as to keep pace with growth of the sector as a whole. In this regard new training institutes be set up and programme to upgrade the existing institutes undertaken.
(ix) The National Institute For Textile Training Research and Design (NITTRAD), a training institute under public sector having necessary infrastructures be upgraded and run under public-private joint partnership with BTMA. This will then be effective and result-oriented. At the moment its performance is below the satisfactory level. If possible this may be affiliated with foreign training institute to impart training to meet the demand of the present day.
(x) Go for capacity building of the textile related trade bodies.
( Views expressed here do not necessarily reflect the views of BTMA or that of government).
....................................................
The author is Secretary-General, BTMA.